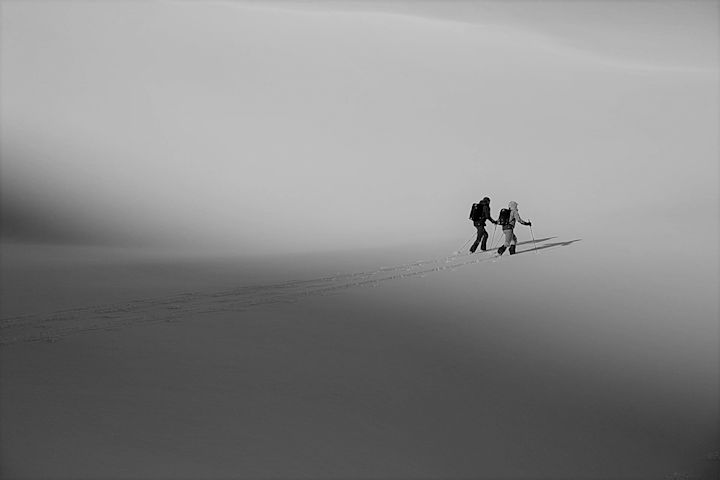
A product failed our
quality check.
What happens now?
September 2023
Ensuring product performance expectations are matched on the nature trail isn’t the only quality test an outdoor product must pass. There is a long series of quality checkpoints each batch of products must make it through—from safety requirements to environmental regulations— before it can be sold to consumers. Sometimes, even after a careful design and production process, products fail. What happens then?
Here, we explain in more detail what kind of quality checks take place during a typical production cycle, and what processes we follow when products fail to pass.
The quality checkpoints a product must pass
Maintaining quality on all fronts is a complex and challenging task. Global outdoor brands must adapt to an ever-evolving landscape of regional and international standards and regulations.
Ensuring that quality is consistently maintained across product batches is accomplished through robust quality control processes throughout the entire production cycle. It involves testing and reviewing materials, components, and finished products to make sure they meet all the required specifications.
Furthermore, many products are audited by a third party, sometimes by the brand’s own service partner, to ensure industry standards are met. Such third party specialists typically spend all day at the factory, performing checks during and after production, referencing against a control sample.
There are a number of quality checkpoints outdoor products must pass before they can reach the hands of consumers, such as:
- Design requirements which ensure that, for example, the sizing, colors, materials, small components like trims and taping, seam length and small visual details correctly match our expectations and standards.
- Safety specifications which ensure that the produced gear can withstand the stresses of outdoor use and protect users from potential hazards.
- Chemical compliance standards which dictate what kinds of material and substance restrictions must be followed in order to minimize harm to the environment, as well as to the people making and ultimately using the product.
So, what happens to products that don’t meet our quality standards?
Considering the vast number of requirements products must meet at every stage of production—from design to manufacturing—sometimes mistakes happen. At Haglöfs, if we discover that a batch of products doesn’t meet our quality standards, there are a number of routes we may take, depending on the circumstances and fixability of the problem.
Scenario 1: The problem is fixable & discovered before the products are released to consumers
In the vast majority of cases, the issue is detected before products even leave the factory and is fixable. When detected in the factory, it is usually rather easy (and not very costly) to address.
In some cases, we detect the problem once the products have reached our warehouse. Then we fix the problem on our end—which is usually more complicated and costly, but usually doable—before the products reach the consumer.
Scenario 2: The problem is fixable & discovered after products are released to consumers
In rare cases, we find out about an issue only after the products have reached stores or the consumer. Then we have to do some detective work (and it’s usually a lot of work).
If we discover that the quality issue is serious according to our standards, but the products otherwise meet the legal requirements, we stop selling the products, inform our customers and consumers, and offer to take back the products for repair or reimbursement. Again, we aim to repair the entire batch of products that remain in the warehouse and then put the repaired products back up for sale.
In the unlikely event we discover that the quality issue does not meet legal requirements, then we must issue a product recall. A product recall entails reporting the issue to the authorities as well as to our customers and consumers. If the recalled products are repairable, we then amend the products and begin selling them again.
Scenario 3: The problem cannot be fixed
In the rare scenario that a product quality issue cannot be repaired, the products cannot be put up for sale again and a decision must be made regarding what to do with them next. Considering that the products have already been produced—and resources have been consumed and carbon dioxide has been emitted in the process of producing them— we believe that it is always better to make sure the products stay the loop to reduce their overall environmental impact. For us, the landfill is never ever an option.
So, if a batch of products is mostly acceptable for use, apart from defects that cannot be fixed—such as a shorter than desired length, or the wrong color on the main material— we will send them to Haglöfs outlet stores and sell them at a reduced price. In some cases, we save the products for donation to charity. And if a batch of faulty products are not suitable for the outlet or donation, in most cases we either save the products so we can later repurpose their components for use in new products, or we take the products apart and recycle them.
What if there is a quality issue with a single product?
The process we have explained here applies to larger batches of products. If a single product should turn out to be faulty, the consumer’s purchase is covered by our warranty process.
We are proud of the quality of our products, so we guarantee to the original owner that should a product, in the course of normal use, fail due to a manufacturing defect, we will repair or replace it.
Learn more about our warranty process here.